Victory is Sweet: The 8” Round Tower
- da'Boss
- Jan 17, 2021
- 12 min read
This has been a very long time coming, but da’Boss is not known to be daunted by even the most impossible of projects. And THIS was a project. *deadpan* In fact it could easily have been seen as 4 projects all wrapped into one, based on the size of the molds he required to make the production of these monstrosities palatable. No, seriously! No sane enthusiast would set out to make a piece this large, and THIS majestic and do it with anything less than the panache of the goblin tinker Himself! *grumble*

So LET me explain! Pull up a seat, sip your coffee, mead or beer *warm please* (goblins like warm beer), and relax while I regale you with the telling of this Epic story!
Back in July of 2020 that damnable year that will go down in history as year of PAIN; The first glimmer of ambition was the moment I found myself in possession of the mold to make the 8” tower. I knew I wanted to make a larger tower after I first made the 3” tower molds, back in January of the same year, of which I have sold several on ebay now. They are smallish and they don’t allow you to PLAY inside much. They are nifty ‘fer sure, but they are almost Small enough to be an accessory for those of us with grandiose notions about terrain and role playing in an immersive experience.
Ha! So there you have it. the goal of the project. Go big or go home. Well... The Goblin Tinker went BIG! 18” tall big!
As you can see the blog posts started in August of last year, as I built the prototype and set out deciding what elements it needed and how to go about building the masters that da’Boss would make the molds out of. Please feel free to peruse those blogs. They definitely capture some of the excitement of the process.
The first obstacle of the process suddenly became clear however. Casting the prototype and designing the masters required days, I mean daaaaaayyysss of casting blocks out of the single mold da’Boss possessed because he is cheap in the most derogatory use of the term. What one will learn is that being CHEAP is a mindset all goblins have. The tinker suffers from this glorious vice along with all his other grandiose delusions! *grumble*
So the toil at the beginning of August found da’Boss toiling in 100 degree heat at the end of summer making the basic bricks that would be glued into the masters. Did I mention the heat? Its fantastic. It reminds da’Boss of the glorious heat of the warrens of his youth and the workshop became a smelly mess to match his youthful days of squalor. Just Brilliant I say! Don’t do this at home, its really NOT recommended. You really must be unhinged by your inner madness and um er.... drive. Yeah. Yeah.....
There is a post of the unprepared master on the blog for you to see the first piece in question Smack dab in the middle of august.
So. What did da’Boss do next, you ask?’
He stared at the master pondering how on earth this could be reproduced. It is the single largest piece I’ve made. It’s even larger than the 4x4 Dungeon intersection I first crafted more than a dozen years ago to emulate the design of the Dwarven Forge resin set for a regular dungeon crawl. That was my first masterpiece of molding genius And I’m still very proud of it! But this first level of the 8” circular tower was LARGER! and not only was it larger, but it had more definition. It had windows. It had a DOOR! And it had ascending stairs to the second level. Oh My God!!! What have I done!!! *facepalm*

So, I set out doing the math per level like I’ve done with the Wizard’s Tower which I cast level by brick level and then assemble with glue to make the entire building. It’s a very functional building. It has 3 levels and a conical roof! This was my best comparison. it took 4 molds to cast and it’s very achievable to cast in a short afternoon and then set out to dry. But after doing the math by each brick level it became clear this was insanity. It would take at least 12-16 molds to make the entire tower and require a ton of assembly. I didn’t like the prospect of this. I didn't feel like it was palatable nor quickly reproducible. Do I hear a *grumble*? Or perhaps a groan? Go ahead. Groan for me.
So da’Boss sat at his workbench and stared at the complexity of his only other solution.
Cast each of the FOUR levels each... in ... one ... piece.....
Mad fucking genius.
I need to pause a moment here for you to let this sink in. HOW on earth can you cast an entire 8” diameter piece that has multiple windows and a door let alone a circular window and door in ONE cast and have it come out of the mold without breaking off the delicate stone above them?! This was a hope despairing obstacle.
*insert audience gasp*
I may have despaired for a smidge. *long distance stare*
Again, why hadn’t someone DONE pieces all in one cast?! Who else was doing this? No one. Was there a reason for this? Probably. Was this difficult? Most definitely. Was this achievable? Doubtful. Is this more costly!! Ha! Who thinks of these things?!?!?! So.
Great. Lets DO this!
So once I became ‘comfortable’ with the idea that the only ‘reasonable’ way to accomplish the goal was to solid cast each of the 4 floors of the tower I then met the obstacle of how to cast each of the floors with their doors and windows.
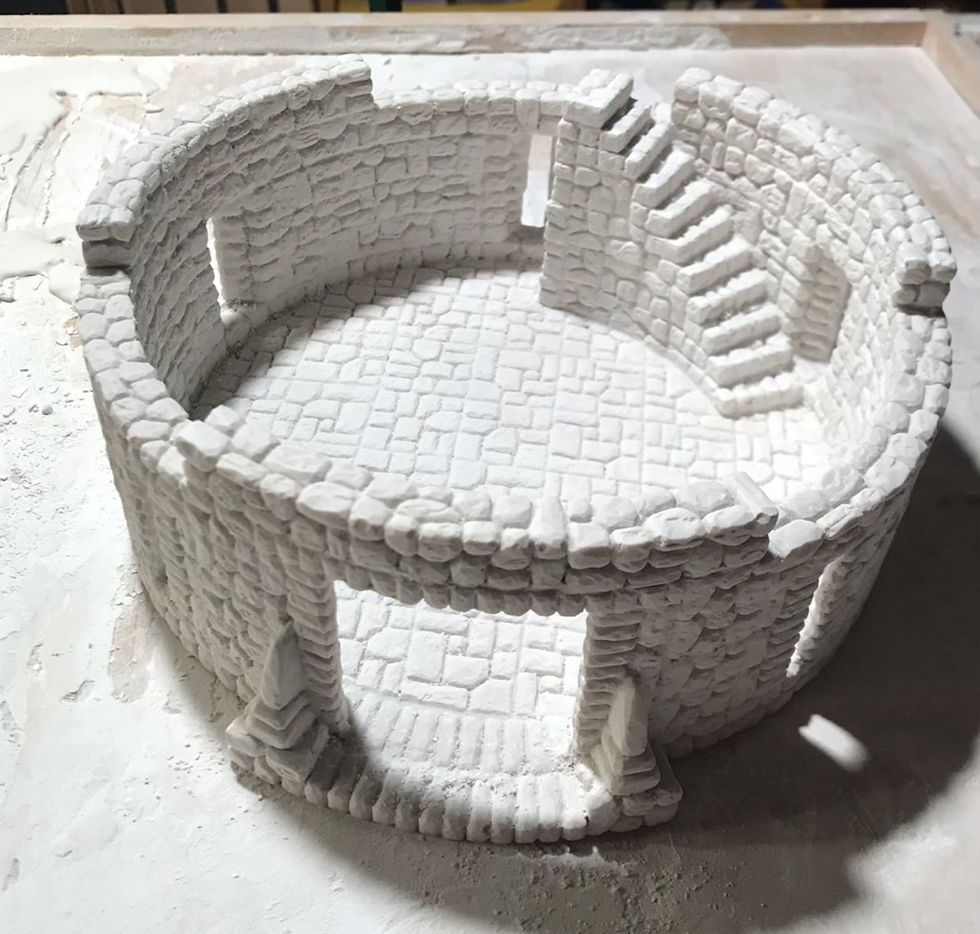
My plan B was to pour an inside mold and an outside mold. The trick was how do you pour an Inside mold and have it not ‘fill’ in the entire inside preventing it from being de-molded without breaking the master let alone the cast. The inside piece needed to contain a void so the silicone could be pulled away from the inside wall. This became obvious Quickly. Easy. Great. Make a void.
Ah, easy you say? Ok let me pause for a moment and negotiate the kinds of molds silicone can make. I doubt this will be exhaustive, but it may be instructive.
The one piece mold is the simplest of molds to pour. It's easy to de-mold and likely is flat. Right?! Ok.
The next step up in complexity is making a two part mold. This requires you to pour one half of the mold by creating a dam to keep the liquid silicone from pouring into the other half or part of the mold. Reasons you may choose this is because its impossible or difficult to de-mold the piece without breaking it or tearing the silicone when first de-molding it or casting the piece. Spherical objects need to be molded with two halves. da’Boss made two piece molds for the 4x4 intersection mentioned before. The inside and the outside. Simple & Easy. This step however doubles the amount of time it takes to make a mold. One day for the first half to cure, I’m using a 24 hour tin or platinum base silicone. FYI. And then another day for the other half to pour and cure. The silicone also needs to be prepared with a mold release so the second pour doesn't cure to the first half.
The next step in complexity is brushing on silicone in multiple levels because the piece has deep undercuts that prevent it from being poured or has vertical and horizontal pieces. This also doesn't use as MUCH silicone as a pour and requires the creation of a mother mold To preserve the form of the malleable silicone Think a bust With a head and chin. This step also requires the silicone be thickened so it can be brushed on and will not drip down like normal fluid from the piece it is supposed to adhere to. It needs A thickener. Brushing on layers of silicone takes several hours to two days for each part of the mold.
The next step in complexity Is crafting a mold that needs to contain a void To make it possible to de-mold an inside piece of the mold vs an outside piece that can be simply pulled away. This also costs less in silicone. Which will become an issue I later detail.
The NEXT step in complexity is creating a mold for a piece that has openings in it. Like a window Or door. This requires the use of a shim, so the silicone does not cure all the way around the ‘hole’ in the subject being cast making it impossible to de-mold from the master. You have to be able to take it apart.
da’Boss was NOT confident this step was achievable, and that the piece would be too difficult to de-mold, and cast if the tops of the walls that created the window and door would be strong enough to de-mold.
*sigh*
So My plan C: was to take each of the tops of the windows and doors off and cast them in a separate mold so the piece could more easily be de-molded. *grumble* This was NOT a satisfying compromise. Let me explain: I spent quite some time researching how to make silicone molds And settled on a method of using a ‘shim’ between each of the window and door treatments to prevent the silicone from curing to each other. but I just wasn't sure it was going to work.
So I spent the entire month of September researching HOW to do the shims. I dithered. I asked questions. I waffled. I changed my mind.
To make a long story.... don’t laugh.... shorter..... I made the decision that despite any doubts to the contrary that If da’Boss didn't take the risk to pour it all at once with all the windows and door, that my curiosity and sense of adventure would just never be satisfied. So to work I went and the consequences be damned.
da’Boss glued the tops of the windows and door back onto the masters and I set to work Estimating how much silicone it would take.
Yup! a lot. I looked at my treasure chest and my very high intelligence immediately told me this was another obstacle. I needed 2 gallons, GALLONS, of silicone. Yikes.
But guess what, not soon after eBay sent me a notification that someone LIKED and BOUGHT enough masterly crafted terrain, a Wizards Tower and A Cottage, to restore my treasure chest to an adequate level!!! Huzzah!
*da’Boss did a goblin jig*
Now, the dice were cast. The silicone traveled over hill and dale across rivers and a mountain range to my humble workshop and there was much celebration.
So what did da’Boss do?
He set to work. He finished preparing the masters for their imminent immersion in silicone and practiced making shims. (This process normally takes 2 days to finish each master, but due to the size of each level of the 8” Tower it took closer to 4-5 days per level.) So, the Shims… He didn't like the first shim. He removed it. Note to self: don't make a shim with epoxy if you don't have something STRONG to remove It. Ugh. He made a second shim. This one was a little better!
da’Boss then set about making the rest of the shims and then set to mixing and brushing on the first Layer of silicone For the inside mold. Inside first and then outside second. its worth noting that da’Boss decided to brush on the inside mold because this would create the void, and then to pour the outside mold for the first level, in one piece Making a two part mold.
Now, when brushing silicone on a mold... you brush on the detail layer first. Yes. Detail is why we do this. The Hirst Arts pieces contain a fantastic level of detail, and the fieldstone pieces are the most difficult to pour because of their countless deep undercuts and dramatic relief. So this first brush is done without, I repeat WITHOUT a thickener. Just mix the silicone and brush it on And let it flow down the piece into all the cracks and nooks. Perfect. Then let it cure a little Before brushing on the thicker thickened layers.
The plan was to brush the inside walls and let the silicone flow to the floor and then pour a little silicone in the floor to insure it had enough thickness to demold without ripping. About 1/2-3/4 an inch of silicone. It took about 5-6 layers of brushing with at least 90-120 minutes between each brushing to let the silicone cure enough to be tacky And stop flowing. At this point the mold looks a lot like a purple dragon’s round sphincter. Don’t ask how I know.
At this point I realized I was running out of catalyst for the silicone at a dramatic rate. da’Boss began to panic. da’Boss ran his glare around the bustling workshop at the gaggle of lackeys who quickly fell silent. “WHO’S EATING MY CATALYST?!!!!“ He roared!
At which point my smartest of lackeys, if ever a lackey can be called smart, picked up the instructions and pointed out da’Boss was mixing the Silicone WRONG!
*da’Boss bangs head on workbench*
*lackeys begin furiously going about their work busily ignoring da’Boss lest they end up as goblin lackey soup*
Of ALL the stupid Mistakes to make when setting about with the delicate balance of chaos and order amidst the crucial capstone of a months long project!!! da’Boss assumed, since this was a tin silicone, that THIS silicone was mixed at the same ratio of the other tin silicones he has used for years. Oops. Nope. RTFM boys. RTFM!
So, after the panic filled room returned to a normal level of panic da’Boss hoped he could squeak out the other gallon’s worth of catalyst between what was left of the first gallon. *sigh* With this out of the way and a plan B set in motion da’Boss let the final brushed on layer cure, he poured the mother mold to fill the inside void of the inside mold and then prepared to pour the outside mold the next day.
The outside mold required the use of a mold box. I made this out of wood Beveled at the corners and slapped it together with a couple rubber bands to keep it in place. It left a gap around the piece of about an inch on each of the sides, and had corners. da’Boss brushed in the detail layer. I poured the mold. I poured another layer of the mold. I looked at how much silicone I had left in the gallon and mixed and poured the rest of it into the mold to fill it to the top! All the while shaking my head that I had underestimated the amount of silicone and I had 3 more levels to cast, a conical roof, AND extra pieces to make the keys to each floor.
Now, at this point you may be questioning da’Boss's genius intellect. But fear not. eBay the ethereal power of the universe and the source of all my bounty came through again With another distant admirer of my diligent craft. Huzzah! I knew I would be able to finish the next 3 floors despite this ‘underestimation’. *grumble*
So now, I will direct you to my last blog post for the reveal of the de-molding of the first master which this article has detailed. It includes a picture of its virgin cast. It was a glorious moment and was met with much celebration. The Lackey’s forgot their near constant state of panic and much wine was poured and many more lackies were whelped.
da’Boss went back to work and brushed on the 2nd and 3rd levels Using the last of the 2nd gallon of silicone, Procured a third gallon of silicone and continued to brush on the 4th level, and poured the conical roof mold, The pieces for the rest of the mold were aggregated together; the door, extra Pieces and a number of columns to fill out the inside decorations of the inside of the Tower, and now here we are.
The 8” circular tower is done! DONE I say! Oh, wait. It needs to be painted. *takes a week to paint it*
It stands 18” tall, almost 22” with a flag on top. It has 14 small windows, it has a double window in the front on the second floor and a small balcony, 1 door, two stone stairs, a Dais on the second floor. The third floor has circular steps to the rear window and small balcony. On the outside the front has 6 ‘teeth’ from the 3” tower mold below its balcony. The third floor balcony in the rear has its balcony supported by the 3” separator for the 3” crenelations. The top of the tower, the 4th floor, is done with a wood floor and the crenelations go all the way around. Each of the floors are solid cast. The 9” diameter conical roof was cast in two molds and is glue assembled together by each level of the descending circular ring.
The Pieces that are not solid cast are the teeth for the 2nd level, the keys for the 2nd, third and fourth floors, the door, and the columns for each floor. There are a couple extra accessories in the bunch.
Da’Boss has decided, because he can, that casts of the 8” tower will be made available on eBay unpainted, AND painted. Huzzah!
NOTE: If any aspiring hobbyists have questions about the gory ‘details’ of the process to make the mold please send me a PM, I will be glad *grumble* to entertain all your…. questions.
Now. Onto the pictures!

A perspective view of the Tower on da’Boss’s workbench!
EDIT: eBay link for Unpainted tower! https://www.ebay.com/itm/D-D-Hirst-Arts-8-Unpainted-Round-Tower-9-x9-x18-Unpainted-Dwarven-forge-/333860946696?_trksid=p2349624.m46890.l49292
This is incredible